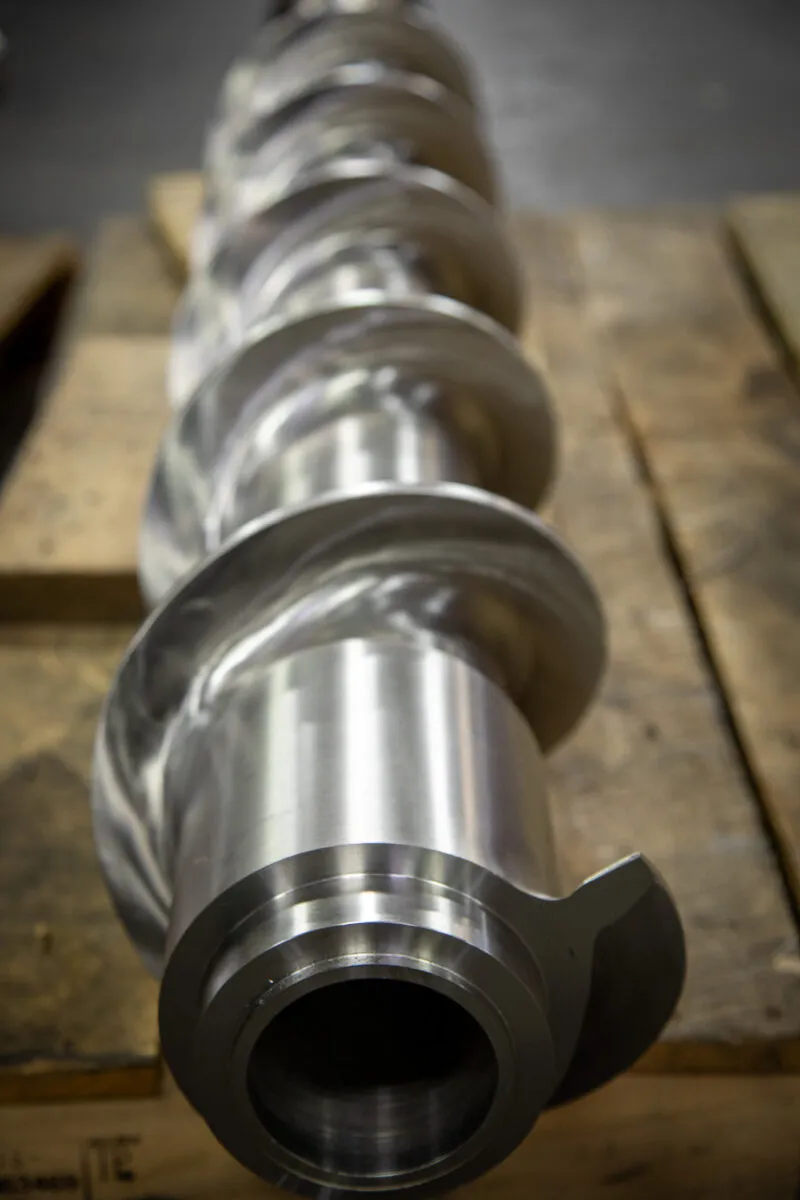
September 7, 2025
An Introduction to Single Screw Extruders
Explore the basics of single screw extruders—how they work, core components, advantages, and common manufacturing applications.
September 7, 2025
Explore the basics of single screw extruders—how they work, core components, advantages, and common manufacturing applications.
September 27, 2024
The Bonnot Company has manufactured a line of extruders for processing butyl/mastic rubbers (butyl) since the 1950's. The company recognized the need to offer processing extruders for this rapidly developing market. In keeping with a core principle of continuous improvement, these designs have evolved over time to remain the pre-eminent industry choice for butyl processing equipment/extruders.
September 19, 2024
The Bonnot Company has a variety of custom extruders designed for bulk feeding of rubbers, both natural and synthetic, silicones, butyls and mastics. Regardless of the batch size or material viscosity, there is a solution available. If one of the company's standard designs does not meet your needs, a custom solution is developed. Customized solutions specifically tailored to a customer's needs are a core competency of ours and competitive advantage.
December 16, 2022
The Bonnot Company's best practice is to conduct testing as there is no reliable theoretical modeling that accounts for all the variable factors in the extrusion process.
July 31, 2020
Over the past few years, many start-ups have approached Bonnot regarding plant-based protein extrusion, looking to capitalize on the increasingly popular trend of marketing meat-free alternatives to consumers. As more people continue to adopt vegan and vegetarian lifestyles, there is a growing need to understand and expand plant-based food processing techniques.
June 16, 2020
It's no secret that Bonnot has been around a long time. We're so old, in fact, that we don't have Articles of Incorporation — they weren't necessary in 1891. But what most people don't know is that we started out making machines to process clay. By the early 20th century we transitioned to brick machines, paving roads for cities across the US, and eventually to the wide catalog of extrusion equipment and machines we're known for around the world today.
June 1, 2020
Rubber granulators have been used for over half a century to resize rubber bales into usable chunks for downstream processing. They are designed to run for many years, which is why they're still prominently used in rubber processing plants. The problem with rubber bale granulators is that they often require the introduction of chemical agents to do that job efficiently. Luckily, Bonnot has the solution — and we have for more than 25 years.
May 4, 2020
As Bruce Sterling quipped at the 1994 Living Surfaces Conference in San Francisco, "Today's solutions are tomorrow's problems." This much is especially true of plastic, which has become one of the most divisive materials of our time. While it was a truly revolutionary material when it was first developed, today it's often looked upon as a nuisance at best and a major environmental threat at worst. However, thanks to recent developments in which The Bonnot Company has played a key role, plastics are starting to become beneficial again. Learn how turning plastics to oil will change the future of multiple industries.
April 1, 2020
The use of hydrocolloids in medical and pharmaceutical applications has been an important development. Because they are a medical implement, hydrocolloids have to be developed and manufactured according to stringent specifications. The Bonnot company has provided extruders for processing hydrocolloids for many of the worlds largest manufacturers. It all begins with hydrocolloid extrusion.