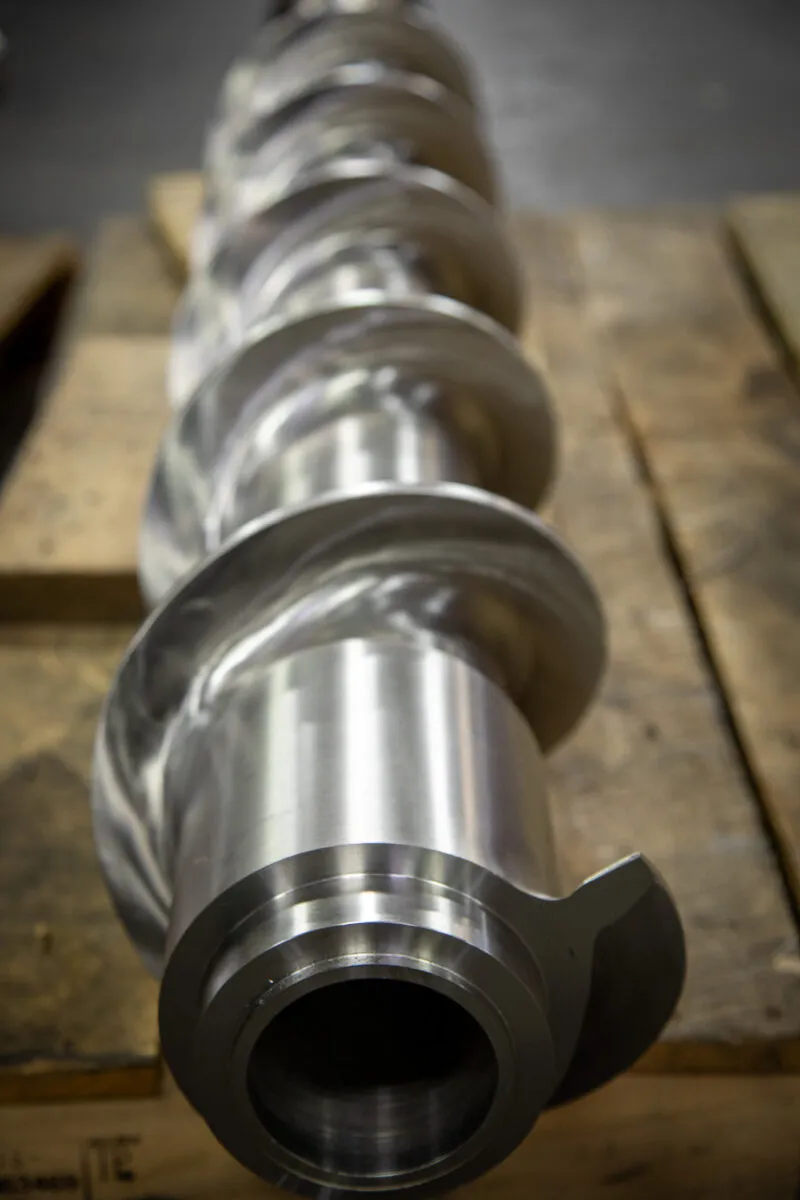
July 9, 2025
An Introduction to Single Screw Extruders
Explore the basics of single screw extruders—how they work, core components, advantages, and common manufacturing applications.
13th February 2020
Increasing efficiency is a must for any manufacturer, but here at The Bonnot Company we’ve had more practice than most in harnessing the power of technology over the course of 128 years in business.
We design, engineer and manufacture extruders, feeders, cutters, and other types of custom processing equipment. We specialize in the custom design and manufacturing of equipment that fulfills very specific needs to solve problems that our customers face.
As the company has been in business since 1891, we serve a fair amount of legacy customers for whom we perform upgrades on existing equipment. We’re able to take older machinery and improve on its design for modern challenges.
One of the ways we look to drive down costs for our customers is via EDGECAM computer-aided-manufacturing (CAM) system — particularly with the production of our augers, or screws.
When we brought in our first piece of CNC equipment 10 years ago, we were doing more hand-programming at the machine for one-off parts.
Notable efficiency gains have been made since the implementation of EDGECAM, including a 50 percent reduction in machining time for our complex and expensive legacy part made from a forging and turned in four axis.
We were able to reduce milling time from 240 hours to 160 hours on a feed screw for the Bonnot Rubber Bale Feeder.
The Bonnot Company uses the SOLIDWORKS® computer-aided-design (CAD) solution, by Dassault Systèmes, to design its parts, and easily imports solid models generated by the system into EDGECAM. Among other machinery are a Haas VF-7 vertical machining center, and two Haas VF-4 vertical machining centers.
All this technology allows as to serve our customers with the best quality, on quick timeline and cost effectively.
Get in touch with the team at Bonnot to learn more.
July 9, 2025
Explore the basics of single screw extruders—how they work, core components, advantages, and common manufacturing applications.
September 27, 2024
The Bonnot Company has manufactured a line of extruders for processing butyl/mastic rubbers (butyl) since the 1950's. The company recognized the need to offer processing extruders for this rapidly developing market. In keeping with a core principle of continuous improvement, these designs have evolved over time to remain the pre-eminent industry choice for butyl processing equipment/extruders.
September 19, 2024
The Bonnot Company has a variety of custom extruders designed for bulk feeding of rubbers, both natural and synthetic, silicones, butyls and mastics. Regardless of the batch size or material viscosity, there is a solution available. If one of the company's standard designs does not meet your needs, a custom solution is developed. Customized solutions specifically tailored to a customer's needs are a core competency of ours and competitive advantage.