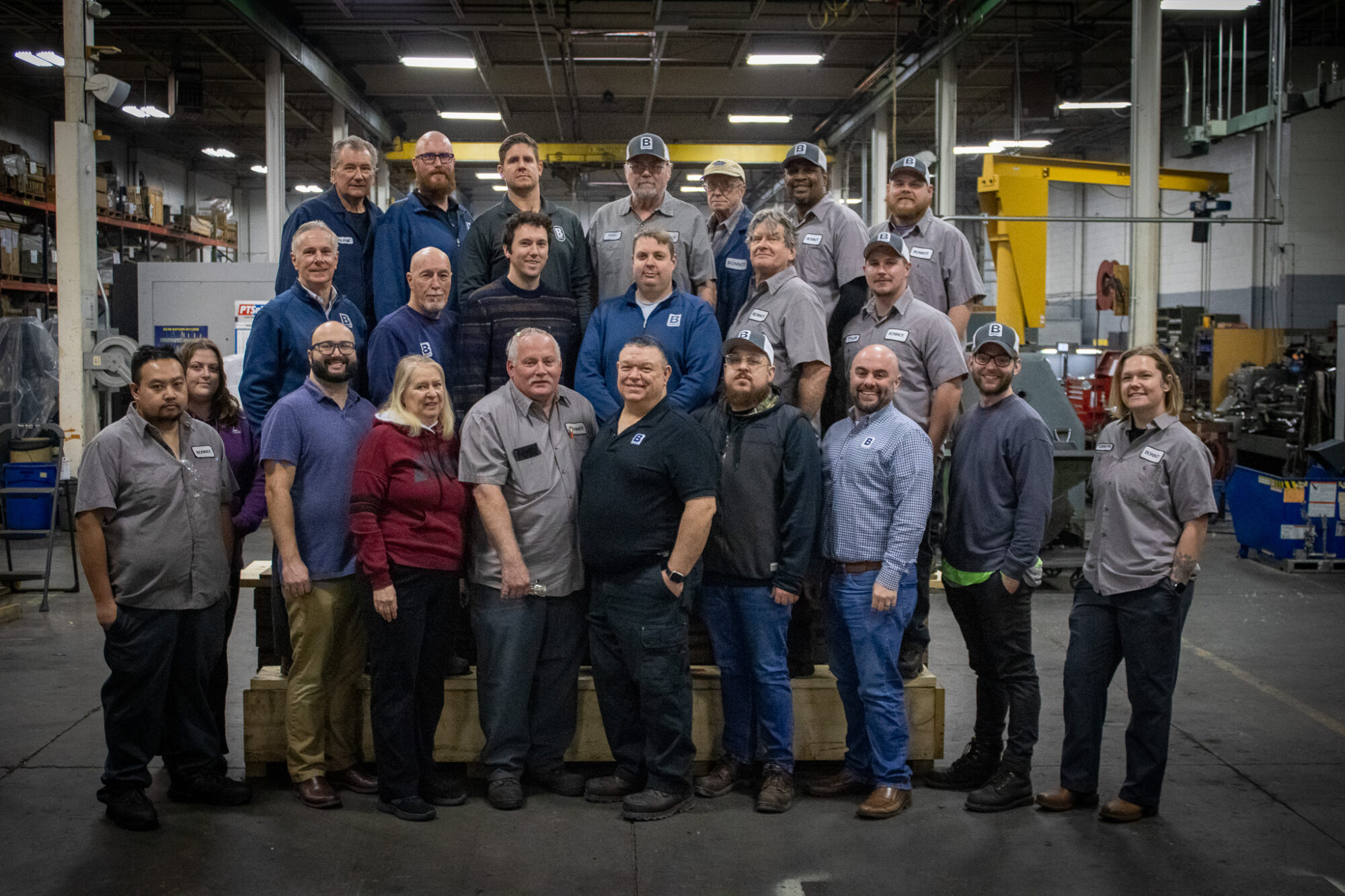
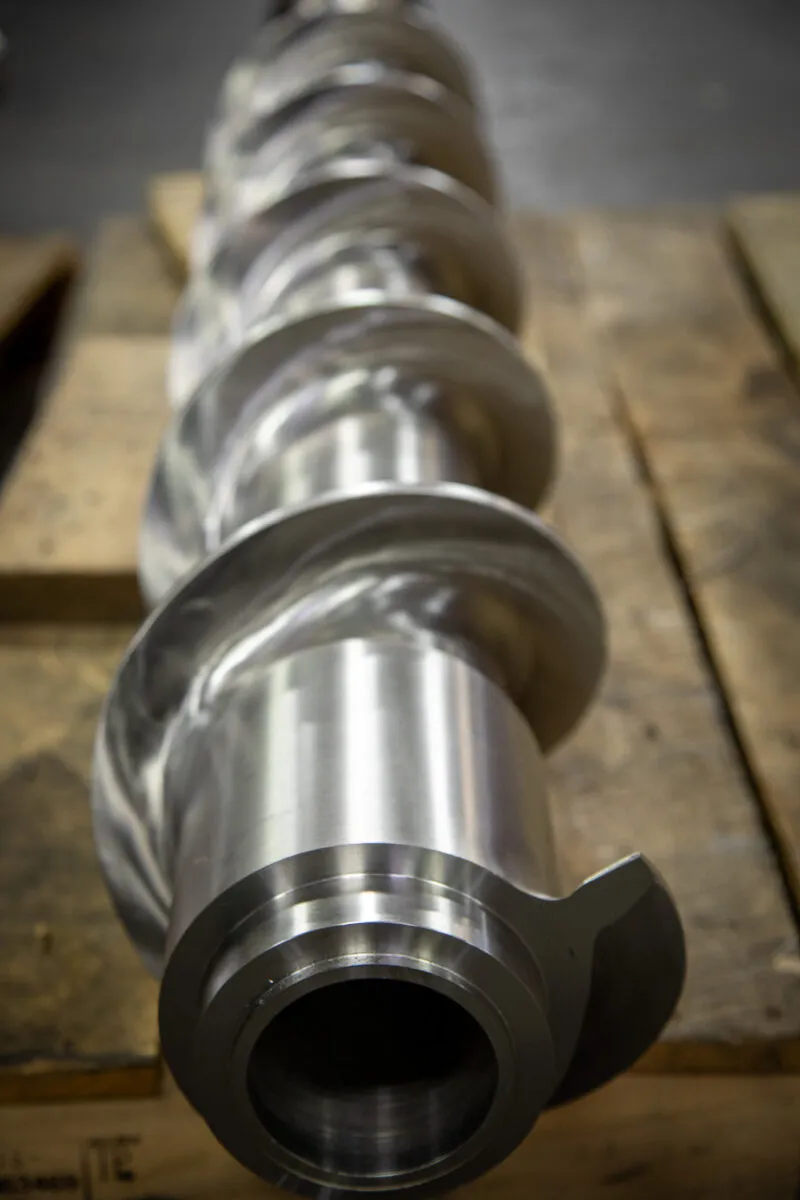
August 20, 2025
An Introduction to Single Screw Extruders
Explore the basics of single screw extruders—how they work, core components, advantages, and common manufacturing applications.
At Bonnot Company, we specialize in the design and manufacture of production quality extruders engineered to meet the demanding manufacturing needs of industries ranging from catalyst and rubber to food production and automotive. With over 130 years of innovation, our extruders deliver the rugged reliability and innovative design you need for consistent, high-quality output.
Quality Policy Statement
The Bonnot Company is pleased to offer FREE feasibility testing in our test facility. Come and take advantage of our comprehensive catalog of test equipment; different extruder designs, screw geometries, forming dies, temperature control options, mixers and material testing equipment.
Get in touch with usAugust 20, 2025
Explore the basics of single screw extruders—how they work, core components, advantages, and common manufacturing applications.
September 27, 2024
The Bonnot Company has manufactured a line of extruders for processing butyl/mastic rubbers (butyl) since the 1950's. The company recognized the need to offer processing extruders for this rapidly developing market. In keeping with a core principle of continuous improvement, these designs have evolved over time to remain the pre-eminent industry choice for butyl processing equipment/extruders.
September 19, 2024
The Bonnot Company has a variety of custom extruders designed for bulk feeding of rubbers, both natural and synthetic, silicones, butyls and mastics. Regardless of the batch size or material viscosity, there is a solution available. If one of the company's standard designs does not meet your needs, a custom solution is developed. Customized solutions specifically tailored to a customer's needs are a core competency of ours and competitive advantage.