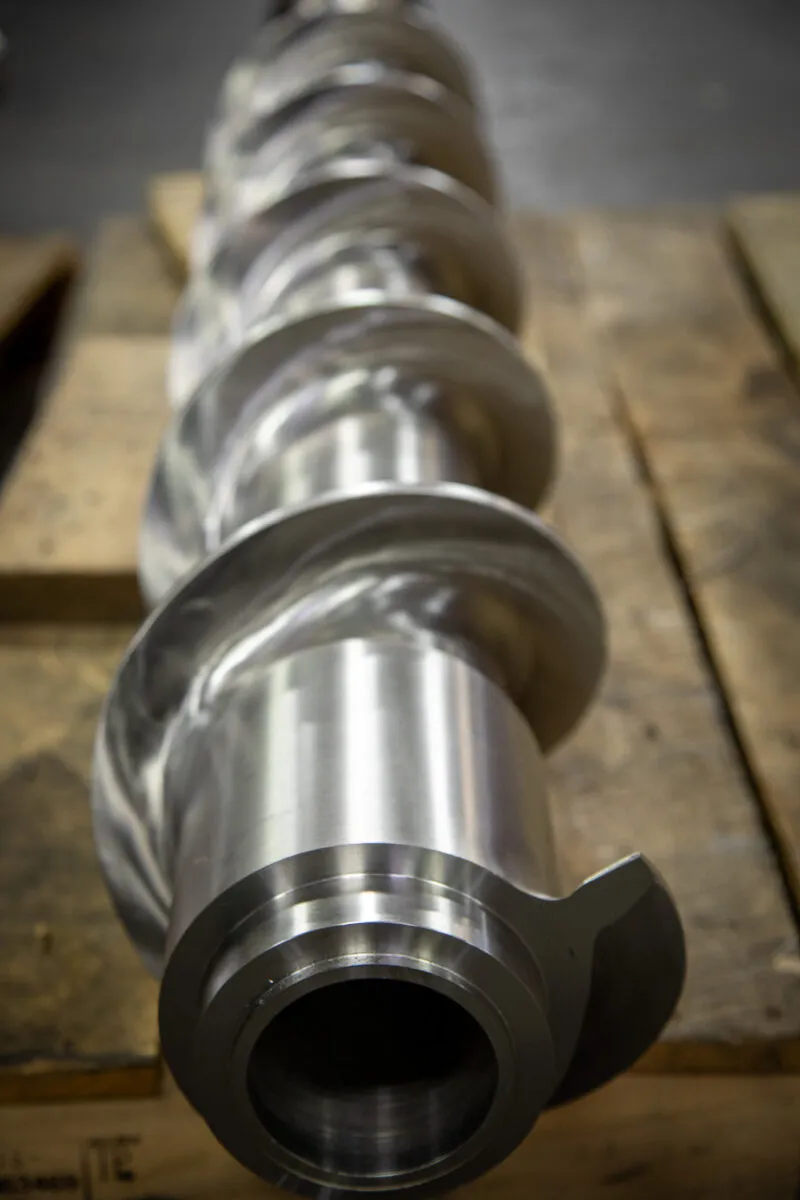
August 26, 2025
An Introduction to Single Screw Extruders
Explore the basics of single screw extruders—how they work, core components, advantages, and common manufacturing applications.
1st April 2020
The use of hydrocolloids in medical and pharmaceutical applications has been an important development. Because they are a medical implement, hydrocolloids have to be developed and manufactured according to stringent specifications. The Bonnot company has provided extruders for processing hydrocolloids for many of the worlds largest manufacturers. It all begins with hydrocolloid extrusion.
Between strict regulations and the specifications of our clients, the Bonnot Company has had plenty of opportunities to innovate in the field of hydrocolloid extrusion. The video below, in which Bonnot Vice President John Negrelli walks us through a complete extrusion system for a medical application, is a prime example:
The machine pictured was created to meet a unique challenge: being able to feed a larger feedstock while retaining the control and metering of a 4″ design, which is standard in hydrocolloid production. We accommodated this need by customizing our 4″ Twin Packer with a 6″ Feed section. Additionally, we plumbed temperature control sections into the hopper, two barrel sections and a commercially purchased state-of-the-art die. To satisfy stringent quality control, a hydraulic screen changer was also incorporated to filter out any impurities as the hydrocolloid material moves through the machine. The system features full touch screen controls and a hand crank to slide it back for easier screw cleaning. It’s a custom solution uniquely equipped for the client’s product while also meeting industry standards and being highly robust and easy to operate.
Whether you require a hydrocolloid extrusion application or something completely different, Bonnot excels at both designing and executing custom extruder machines and parts in our onsite R&D facility. When designing an extruder for medical applications, such as hydrocolloid extrusion, we have a breadth of capabilities at our disposal:
Your search for the perfect hydrocolloid extrusion solution ends with us. Contact our team today to learn more about our custom engineering and design services and take advantage of our combined 200+ years of extrusion expertise. If an extruder could benefit your company, contact us today to get a custom quote on a Bonnot extruder. We’re eager to partner with you!
August 26, 2025
Explore the basics of single screw extruders—how they work, core components, advantages, and common manufacturing applications.
September 27, 2024
The Bonnot Company has manufactured a line of extruders for processing butyl/mastic rubbers (butyl) since the 1950's. The company recognized the need to offer processing extruders for this rapidly developing market. In keeping with a core principle of continuous improvement, these designs have evolved over time to remain the pre-eminent industry choice for butyl processing equipment/extruders.
September 19, 2024
The Bonnot Company has a variety of custom extruders designed for bulk feeding of rubbers, both natural and synthetic, silicones, butyls and mastics. Regardless of the batch size or material viscosity, there is a solution available. If one of the company's standard designs does not meet your needs, a custom solution is developed. Customized solutions specifically tailored to a customer's needs are a core competency of ours and competitive advantage.