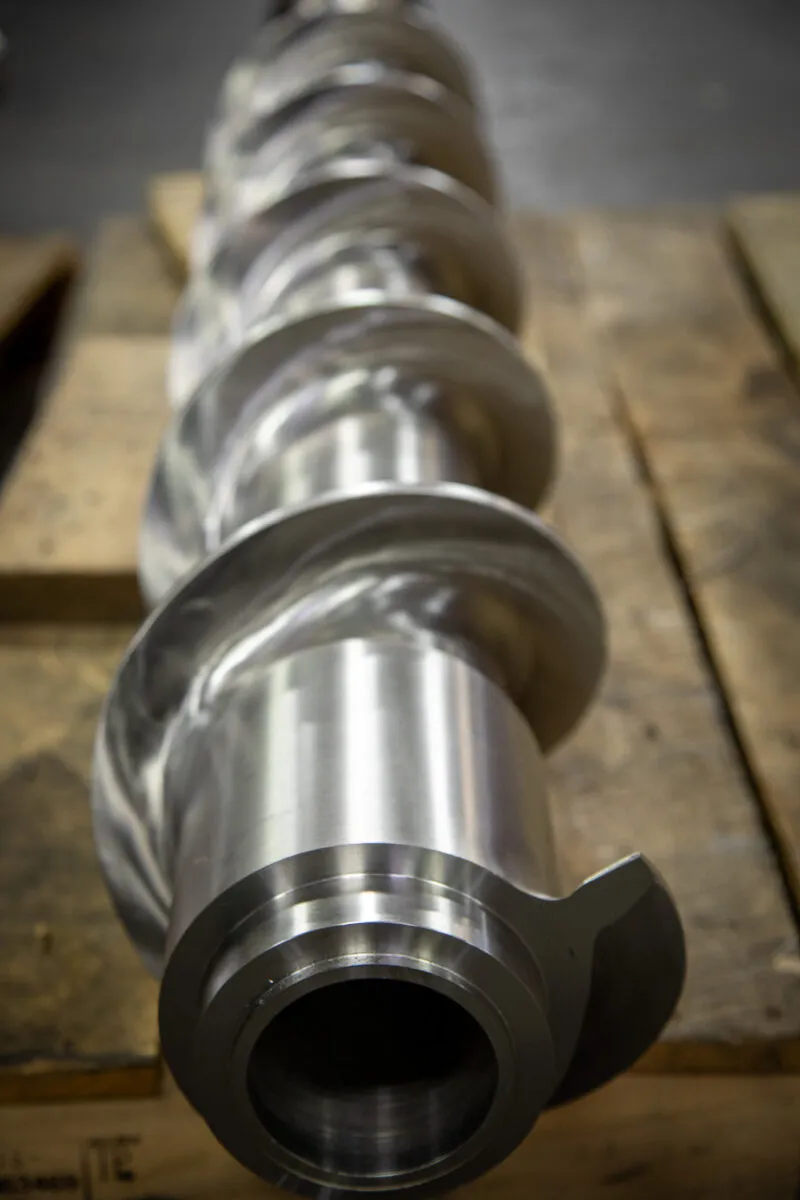
July 18, 2025
An Introduction to Single Screw Extruders
Explore the basics of single screw extruders—how they work, core components, advantages, and common manufacturing applications.
21st August 2019
Working in the rubber industry is a challenging job, and it can be particularly dangerous for the people who work with the rubber directly. But the rubber industry has come a long way in its 130 years of existence — and the Bonnot Company has seen all those changes firsthand. On top of ensuring your facility always operates at peak productivity, safety considerations in extrusion are a high priority when we design our extruders, cutters, bulk feeders and more.
Having to manually handle and cut rubber bales is one of the leading causes of injury at rubber plants. Cutting or granulating rubber bales has generally been a necessary part of processing, however, since some extruders have difficulty breaking down large quantities at a time.
With a Bonnot rubber bale feeder or live bottom extruder, the issue of breaking down bales is eliminated. Our modern, field-tested design ingests partial and full-sized rubber bales to push them through the rest of the extrusion process easily and efficiently. Thus, rubber extrusion safety improves since the machine does all of the hard and dangerous work.
Talc has traditionally been used to help in the granulation and dissolution process of rubber. Recently, it has come to light that the fibers of talc break down similarly to asbestos and may cause similar health issues, such as mesothelioma, after long exposure.
Bonnot extruders completely negate the need for chemicals. Our live bottom extruders break down massive batches of rubber (up to 3,500 pounds) using a system of jacketed barrels and feed augers. The rubber is processed just as effectively even without talc and other chemicals. And more importantly, plant workers are no longer exposed to potentially harmful chemicals.
When considering extrusion safety, it is easy to forget that noise can be just as harmful to workers as dealing with harsh chemicals and unwieldy materials. Hearing damage from exposure to loud noises is irreversible in the long-term, and in the short-term can cause issues like tinnitus and unhealthy levels of sustained stress.
Along with not requiring chemical or manual assistance, Bonnot extruders also do their jobs much more quietly than traditional machines. Extruders and rubber bale feeders produce sound at a much lower decibel level than granulators, which are often used for breaking down rubber bales.
There are several other safety considerations in extrusion that the Bonnot Company takes into account with every machine we create or help our clients develop for their unique needs. If you want to save money, optimize productivity and improve the safety of your rubber plant, you want a Bonnot extruder machine in your facility. Learn more about our rubber bale feeders, live bottom extruders and other machinery, and how Bonnot can help create and test your custom solution.
July 18, 2025
Explore the basics of single screw extruders—how they work, core components, advantages, and common manufacturing applications.
September 27, 2024
The Bonnot Company has manufactured a line of extruders for processing butyl/mastic rubbers (butyl) since the 1950's. The company recognized the need to offer processing extruders for this rapidly developing market. In keeping with a core principle of continuous improvement, these designs have evolved over time to remain the pre-eminent industry choice for butyl processing equipment/extruders.
September 19, 2024
The Bonnot Company has a variety of custom extruders designed for bulk feeding of rubbers, both natural and synthetic, silicones, butyls and mastics. Regardless of the batch size or material viscosity, there is a solution available. If one of the company's standard designs does not meet your needs, a custom solution is developed. Customized solutions specifically tailored to a customer's needs are a core competency of ours and competitive advantage.