An Introduction to Single Screw Extruders
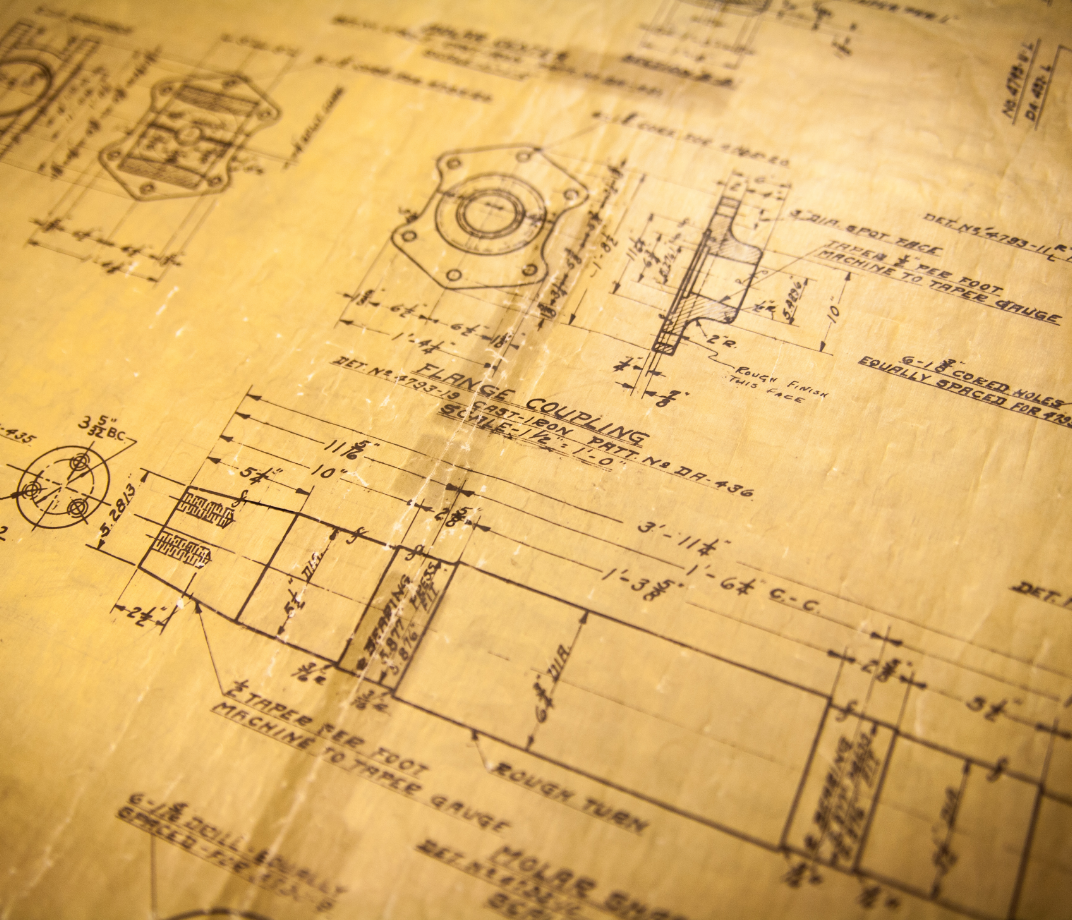
Introduction
In the world of product manufacturing, extruder processing and material forming are critical to many applications. Among various types, the single screw extruder stands out as the most widely used and versatile option. Whether you’re creating pellets, sheets, logs, or other profiles, a single screw extruder often plays a central role in the production process. In this blog, we’ll introduce you to the basic principles, components, and applications of single screw extruders.
What is a Single Screw Extruder?
A single screw extruder is a machine used to form materials into continuous profiles. It consists of a single rotating screw housed inside a cylindrical barrel. The material (usually in the form of chunks, dough or powder) is fed into the barrel and then forced through a die to create a specific shape.
Key Components
Here are the main parts of a single screw extruder:
• Hopper: Where material is fed into the machine.
• Barrel: A cylindrical chamber that contains the screw.
• Screw: A rotating metal shaft with a helical flight, responsible for moving, compressing, and forming the material.
• Die: The component at the end of the extruder that shapes the material into the final product.
How It Works
The extrusion process can be broken down into three primary zones along the screw:
1. Feed Zone: The material is fed from the hopper and begins moving along the screw.
2. Compression Zone: The material is compacted, friction increases, and shear forces create desired material characteristics.
3. Forming Zone: The material is pushed at a consistent rate out of the die.
Once the material exits the die, it may be cooled and cut, rolled, or otherwise processed, depending on the desired product.
Advantages of Single Screw Extruders
• Simplicity: Fewer components and easier to operate compared to twin-screw designs.
• Cost-Effective: Lower capital and maintenance costs.
• Reliable for Homogeneous Materials: Ideal for processing pure or single-type materials.
• Versatile: Used in numerous applications including pellets, film, logs, and other product production.
Limitations
While single screw extruders are incredibly useful, they’re not suitable for every application. For example:
• They struggle with mixing different materials or additives.
• They are not able to accommodate multiple process steps in-line
Common Applications
• Chemical Catalysts Pellet Production
• Adhesives and Sealant Strips or Tape
• Pet Food, Cereals, Protein Products and Chewing Gum
• Activated Carbon Products
• Rubber Bale Handling
• Rodenticide, Bulk Moulding Compound and many more.
Conclusion
The single screw extruder is a foundational technology in the manufacturing industry, offering a balance of performance, simplicity, and cost-effectiveness. For many standard processing tasks, it remains the go-to choice. As materials and manufacturing demands evolve, understanding the basic mechanics and capabilities of this equipment is essential for engineers, operators, and designers working in production.
Contact Us
With a full line of butyl extruders, The Bonnot Company welcomes the opportunity to serve your needs. Please contact us if we can be of any service.